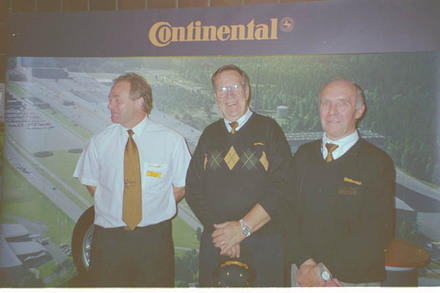
Lördagen den 22 september gjordes i regi av UBCC i Göteborg (United British Car Clubs) ett studiebesök hos Continental Däck i Gislaved.
I samband med British Car Week i maj skänkte Conti generöst ett mycket fint rallypris och då knöts kontakten med Göran Allanson som är säkerhetschef på företaget. Det gjordes en förfrågan om ett studiebesök skulle vara möjligt. Göran som för övrigt har en Mini och således har ett gammelfordonsintresse tyckte det skulle vara trevligt om vi gästade Gislaved.
Vi var över 20 från olika klubbar som tog oss dit i samlad trupp samt några som körde från Varberg och trakten däromkring. Vädret var lite oroligt så de flesta valde att åka vardagsbil. Göran kunde tyvärr inte medverka då han var utomlands utan Bruno Mårtensson som jobbar inom Teknisk Support tog emot oss och lotsade oss till lektionssalen. Dessförinnan hade vi sett att man hissat den engelska flaggan oss till ära.
Bruno berättade lite om fabrikens bakgrund och visade en liten filmsnutt.
I slutet av 1800-talet grundades fabriken av bröderna Gislow och man tillverkade bland annat galoscher och studsbollar. I och med att bilförsäljningen ökade blev efterfrågan på däck större och 1905 tillverkades det första svenska däcket av Gislaveds Gummi.
Utvecklingen av material och mönster skedde kontinuerligt och i slutet av 60-talet var Gislaved en av tre däcktillverkare som började tillverkningen av stålradialdäck.
Ungefär samtidigt byggdes den nuvarande fabriken. Den har en längd av imponerande 640 meter och en bredd av 66 meter. Kapaciteten är ca 4 miljoner däck/år och av dessa går ungefär 80% på export. Efterfrågan på vinterdäck ökar i övriga Europa Man använder i runda tal 28000 ton gummiblandning/år och varianterna är runt 270 st. Märken som tillverkas är Continental, Gislaved, Uni Royal, Semperit och Barum. Biltillverkare räknas till de största kunderna. Personalen uppgår till cirkaa 800 och ett 20-tal nationaliteter är representerade. KF drev fabriken under ett antal år men ägs numera av Continental AG i Tyskland tyska banker, BMW och Mercedes.
I USA finns 5 fabriker och i Rumänien har en ny fabrik uppförts som är tre gånger större än den i Gislaved. Bruno berättade att det finns 30 olika gummiblandningar och ett däck består av många lager som alla har olika blandningar. Någon frågade om 16 däck var bra att använda och fick svaret att de onekligen har en kortare bromssträcka och bättre stabilitet men är lite av mode och användaren blir inte glad när det skall investeras i nya. En annan fråga ställdes om störande vägljud och Bruno menade att de problem som finns i Sverige beror på dåligt underhåll av vårt vägnät. I exempelvis Tyskland har man inte alls detta problem.
På frågan om vad de anser om olika tidningars däcktester tycker de att dessa i allmänhet är ganska tillförlitliga men testerna görs i regel under 1 dag och under samma förhållanden och med samma temperatur. Gislaved gör mycket mer omfattande tester under lång tid och under olika körförhållanden. Det finns en liten bana i närheten av fabriken där vattenplaning testas.
Efter denna genomgång delade vi upp oss i tre grupper för visning av fabriken som just startat helgproduktionen. Förutom Bruno togs vi om hand av gentlemännen Evert Karlsson och Göran Axelsson som båda har ett långt förflutet i företaget men som numera har inträtt i pensionsåldern.
Vi började i den ena änden av fabriken där de olika elementen produceras och som sedan skall utgöra däcket. Maskinparken består av ett stort antal specialmaskiner och man förstår vilket tänkande det ligger bakom invecklade konstruktioner. Man förstår också det designarbete som föregår däckets tillkomst. Många moment skall passa ihop för att få ett trafiksäkert, slitstarkt och miljövänligt däck och man ställer sig onekligen frågan när tar mönstren slut? Men det är väl som med musik, nya låtar komponeras jämt. En del arbetsmoment sliter på kroppen och därför cirkulerar personalen vilket även för det goda med sig att flexibiliteten blir stor.
När vi guidats färdigt i denna del av fabriken fortsatte vi till den så kallade Byggplatsen som är en direkt fortsättning på materieltillverkningen. Detta är unikt i branschen. Som namnet säger byggs däcket här med sina olika komponenter till ett färdigt däck. Även här görs arbetsmomenten vid stationer med hjälp av sinnrik utrustning. Ett däck är tungt att lyfta och därför används robotar. Färdiga däck synas noggrant och ej godkända skärs upp med kniv för att de inte skall kunna komma ut i oseriös handel. De transporteras därefter till värmeverk.
En imponerande anläggning är det så kallade höglagret. Dit transporteras de färdiga däcken på vagnar som sedan lyfts av en specialhiss på spårbunden bana ända upp till 29 meters höjd. Detta sker datoriserat och ingen människa finns där inne.
Miljöaspekterna prioriteras och man gör ständigt förbättringar och tidigare sotiga och illaluktande områden är i stort sett borta. Man frapperas också av renligheten i fabriken och golven är blanka och rena.
Personalvården ägnas också stor omsorg.
Besöket närmade sig nu sitt slut och åtminstone jag har nu större förståelse för att ett bra däck måste få kosta en slant. Vi tackade de tre herrarna för ett mycket givande besök med en varm applåd och vi fick mottaga varsin keps som vi kan varva med våra klubbdito.
Lennart Brick, MG-Klubben
PS Det kan nämnas att Bruno har ett förflutet som tävlingsförare med Volvo Amazon med titlar inom Stockholms Sportvagnsklubb.